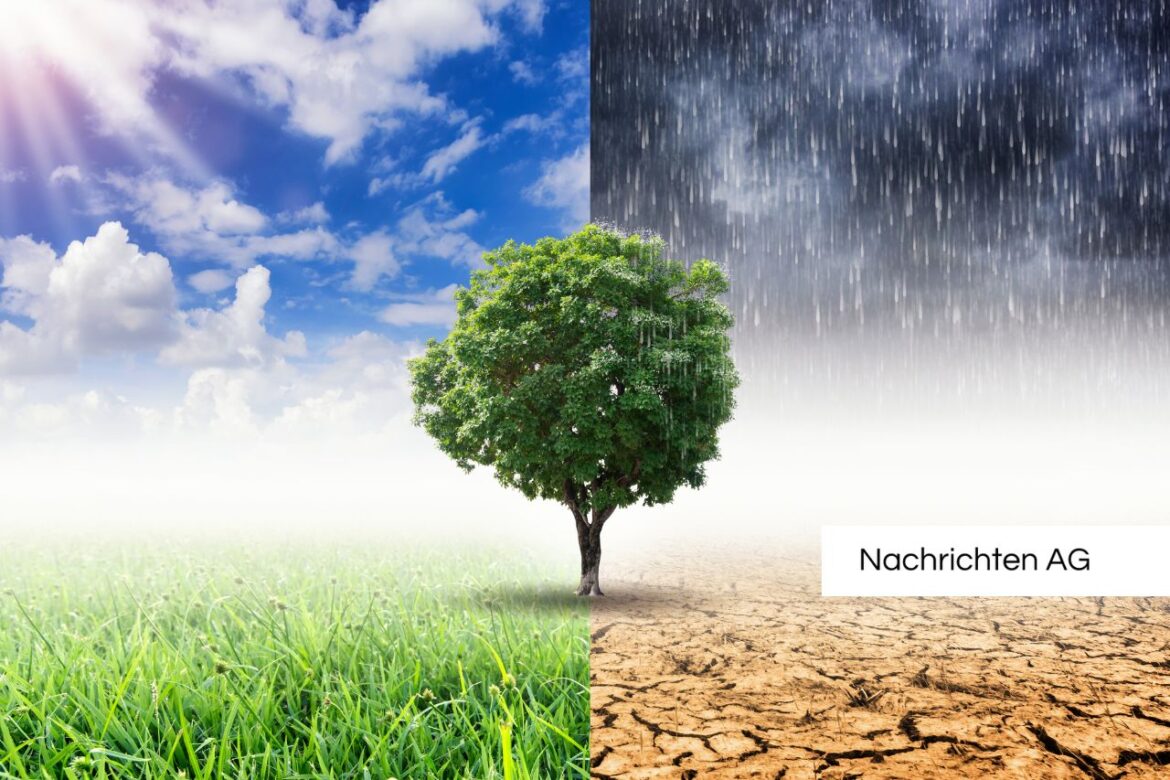
Die Industrie sieht sich zunehmend mit steigendem Energieverbrauch und den damit verbundenen hohen Kosten konfrontiert. Dies hat weitreichende Auswirkungen auf das Klima und die wirtschaftliche Effizienz von Unternehmen. Auf der bevorstehenden Hannover Messe, die vom 31. März bis 4. April stattfindet, präsentieren die Professoren Stefan Seelecke und Paul Motzki von der Universität des Saarlandes eine innovative Robotertechnologie. Diese nutzt Formgedächtnistechnik und verspricht, die Energieverbrauch von industriellen Roboterarmen um bis zu 90 Prozent zu reduzieren.
In der Industrie sind die herkömmlichen pneumatischen Greifsysteme laut und energieintensiv. Zudem stoßen sie bei der Miniaturisierung und Umprogrammierung an Grenzen. Mit Hilfe von Formgedächtnismaterialien, die weitaus leistungsfähigere und flexiblere Robotergreifer ermöglichen, sollen diese Probleme gelöst werden. Die neuen Prototypen umfassen Vakuumgreifer und Zangengreifer, die eine energielose und sichere Handhabung von Werkstücken ermöglichen.
Technologie und Antriebssysteme
Die Robotertechnologie greift auf voll elektrische Greifsysteme zurück, die Bündel aus Nickel-Titan-Draht als künstliche Muskeln verwenden. Nickel-Titan-Legierungen sind bekannt für ihre bemerkenswerte Fähigkeit, bei Stromimpulsen zu reagieren. Ein Draht mit einer Dicke von nur 500 Mikrometern kann über 10 Kilogramm ziehen. Insbesondere konnte ein Weltrekord aufgestellt werden, bei dem 20 Drähte mit einem Durchmesser von 25 Mikrometern eine Zugkraft von 5 Newton bei 200 Hertz erreichen.
Die an der Universität des Saarlandes entwickelten elastischen Greifsysteme sind in der Lage, sich dynamisch an unterschiedliche Werkstücke anzupassen, ohne zusätzliche Sensoren. Der Zangengreifer-Prototyp kann skalierte Greifkräfte von bis zu 4 Newton erreichen, und der Vakuumgreifer generiert ein tragfähiges Vakuum durch kurze Stromimpulse. Diese Innovationen erweitern die Möglichkeiten der Umprogrammierung während des Produktionsprozesses erheblich.
Potenzial der Formgedächtnistechnologie
Die Formgedächtnistechnologie (FGL) hat vielfältige Anwendungen, nicht nur in der Robotik, sondern auch in Bereichen wie der Medizintechnik, Automobilindustrie und Luft- und Raumfahrt. FGL ermöglichen es Materialien, ihre ursprüngliche Form nach Verformung wieder einzunehmen. Diese Technologien sind besonders beliebt, da sie reversible Dehnungen von 8-10% erlauben und durch ihre spezifischen Legierungszusammensetzungen an verschiedene Anforderungen angepasst werden können. Beispielsweise können neue Legierungen, die aus Nickel, Mangan und Gallium bestehen, höhere Schaltfrequenzen von bis zu 1000 Hz ermöglichen.
Im Vergleich zu herkömmlichen elektromagnetischen Systemen bieten FGL eine Gewichtseinsparung von bis zu 80%. Ingenieure arbeiten daran, diese Technologien weiter zu verbessern, um eine noch breitere Palette an Anwendungen anzubieten, von katheterführenden Drähten bis hin zu automatisierten Ventilen, die temperaturabhängig arbeiten.
Die Zukunft der Formgedächtnistechnologie
Die Prognosen für die Formgedächtnistechnologie sehen vielversprechend aus, mit einer wachsenden Nachfrage in der Industrie. Es bestehen jedoch Herausforderungen, insbesondere hinsichtlich der Erweiterung des Temperaturbereichs und der Schulung von Konstrukteuren im Umgang mit FGL. Der technologische Fortschritt könnte die Kosten für diese Technologien senken, während herkömmliche Systeme teurer werden. Unternehmen wie die neugegründete mateligent GmbH übernehmen eine Schlüsselrolle bei der praktischen Umsetzung dieser Technologien.
Das Zentrum für Mechatronik und Automatisierungstechnik (ZeMA) in Saarbrücken spielt eine wesentliche Rolle bei der Förderung des Technologietransfers zwischen Forschung und Industrie. Auf der Hannover Messe suchen die Forscher nach Partnern, um ihre Ideen weiter zu entwickeln und die effektivsten Lösungen für die Industrie bereitzustellen.